طراحی و مهندسی معکوس
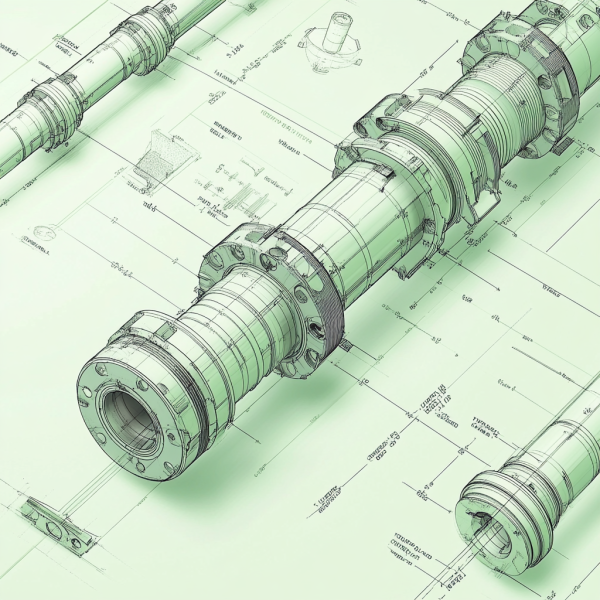
مهندسی معکوس قطعات و تجهیزات، به عنوان یک راهکار استراتژیک در فرآیندهای صنعتی، نقشی حیاتی در افزایش بهره وری و تضمین پایداری تولید ایفا می کند. این رویکرد به صنایع کمک می کند تا در بازار رقابتی امروز، تولیدی پویا، کارآمد و پایدار داشته باشند.
شرکت یکتا انتخاب سرافراز با تکیه بر دانش فنی و تجربه ارزشمند کارشناسان خود، طیف گسترده ای از مزایا و خدمات منحصر به فرد را در حوزه مهندسی معکوس به صنایع ارائه می دهد که در ادامه به تفصیل شرح داده خواهد شد.
1- کاهش هزینهها و دسترسی به قطعات خاص و نایاب
با استفاده از مهندسی معکوس، کارشناسان این شرکت قادرند هزینه های تولید را به طور چشمگیری کاهش دهند و هم زمان دسترسی به قطعات خاص و نایاب را ممکن سازند. این فرآیند، نه تنها تأمین قطعات را تسهیل می کند، بلکه موجب صرفه جوییهای قابل توجه در طولانی مدت خواهد شد.
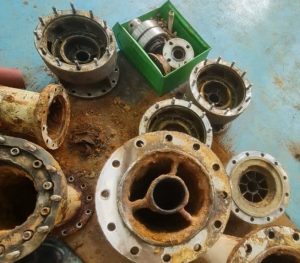
2- تولید قطعات یدکی برای تجهیزات قدیمی و نایاب
در صنایع سنگین نظیر نفت، گاز، پتروشیمی، فوالد و سیمان، بسیاری از تجهیزات و ماشین آلات قدیمی به دلیل محدودیت در دسترسی به قطعات یدکی با چالش های جدی مواجه هستند. در چنین شرایطی، کارشناسان شرکت یکتا انتخاب سرافراز با بهره گیری دانش مهندسی معکوس، راه حل هایی مؤثر، اقتصادی و عملی ارائه می دهند که این چالشها را برطرف می سازد.

3- بازسازی و بهینه سازی تجهیزات برای افزایش کارایی
در بسیاری از صنایع سنگین، تجهیزات به دلیل طراحی قدیمی یا فرسودگی ناشی از استفاده طولانی مدت، ازعملکرد بهینه فاصله گرفته اند. در این شرایط، کارشناسان این شرکت با بهره گیری از دانش مهندسی معکوس،نقش کلیدی در بازسازی این تجهیزات و ارتقای کارایی آنها ایفا می کنند و راهکارهایی نوآورانه برای بازگرداندن تجهیزات به حداکثر بهره وری ارائه می دهند.

4- شبیه سازی فرآیندها و تجهیزات برای پیشبینی و بهبود عملکرد
کارشناسان شرکت یکتا انتخاب سرافراز با بهره گیری از دانش مهندسی معکوس، نه تنها در تولید قطعات تخصص دارند، بلکه توانایی شبیه سازی فرآیندهای پیچیده صنعتی را نیز دارا هستند. این شبیه سازیها امکان بررسی و آزمایش شرایط مختلف عملیاتی را فراهم می کند، بدون آنکه نیازی به اجرای واقعی آنها باشد. چنین رویکردی به بهبود عملکرد، کاهش ریسکها و دستیابی به نتایج دقیقتر کمک شایانی می کند.

5- استخراج استانداردهای فنی و بهبود آنها
کارشناسان شرکت یکتا انتخاب سرافراز با تحلیل دقیق و استخراج استانداردهای فنی قطعات و تجهیزات، به طورمؤثر فرآیندهای تولید را به روز کرده و بهبود می بخشند. این روش، به ارتقای عملکرد و افزایش بهره وری در تمامی مراحل تولید کمک می کند و امکان دستیابی به استانداردهای معتبرتر جهانی را فراهم می آورد.
6- افزایش عمر مفید تجهیزات
کارشناسان شرکت یکتا انتخاب سرافراز با بهره گیری از روش های پیشرفته مهندسی معکوس، می توانند عمر مفید تجهیزات را به طور قابل توجهی افزایش دهند. این فرآیند، به معنای استفاده بهینه از منابع، کاهش هزینه های نگهداری و بهبود پایداری سیستمها در درازمدت است.

7- انعطاف پذیری در نگهداری و تعمیرات
کارشناسان این شرکت با استفاده از مهندسی معکوس، این امکان را برای شرکت ها فراهم می آورند که تجهیزات قدیمی خود را سریع تر و مؤثرتر و بدون نگرانی از کمبود قطعات یدکی تعمیر و نگهداری کنند . این رویکرد باعث افزایش کارایی و کاهش زمان های توقف تولید می شود.
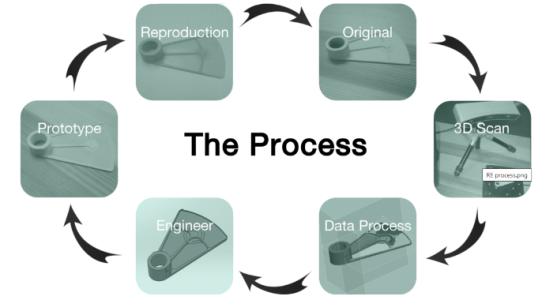
8- نوآوری در طراحی و ایجاد مزیت رقابتی
با بهره گیری از توانمندی های مهندسی معکوس، کارشناسان این شرکت قادرند طراحیهای نوآورانه ای برای تجهیزات ارائه دهند که کارایی، به روزرسانی و پیشرفته تر بودن آن ها را بهبود بخشد. این نوآوری ها، به شرکت ها کمک می کند تا مزیت رقابتی چشمگیری در بازارهای صنعتی کسب کنند.
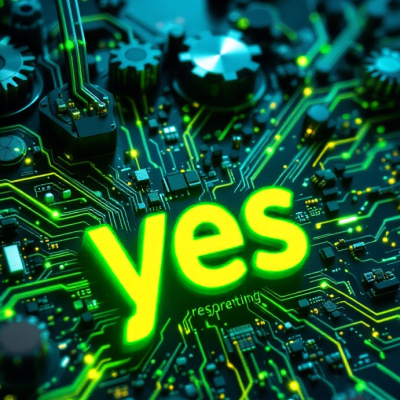
مراحل مهندسی معکوس و فرایند ساخت و کنترل قطعات و تجهیزات در شرکت یکتا انتخاب سرافراز
الف - جمعآوری اطلاعات اولیه و شناسایی نیازها
اولین مرحله در فرآیند مهندسی معکوس، شناسایی دقیق هدف از انجام این فرآیند است. این هدف ممکن است شامل بازسازی قطعه، تولید انبوه یا بهبود عملکرد آن باشد. در این مرحله، مهندسین و طراحان شرکت یکتا انتخاب سرافراز با دقت و به طور جامع، ااطلاعات اولیه را از طریق بررسی دقیق قطعه فیزیکی جمع آوری می نمایند:
دریافت قطعه: قطعه اصلی که قرار است مهندسی معکوس شود، باید به طور کامل مورد ارزیابی و تجزیه و تحلیل قرار گیرد. در صورتی که قطعه حاوی علائم یا اطلاعاتی از شرکت تولیدکننده باشد، این داده ها می توانند به عنوان مبنای اولیه برای تجزیه و تحلیلهای عمیق تر و تصمیم گیری های آتی به کار گرفته شوند.
تعریف نیازهای فنی: در این مرحله، ضروری است که بررسی شود هدف از مهندسی معکوس، تولید قطعه جدید است یا هدف از آن تعمیر و بهینه سازی قطعه قبلی می باشد. این بررسیها با هدف شفاف سازی دقیق نیازهای فنی، مسیر اجرایی بهینه فرآیند مهندسی معکوس را مشخص کرده و تضمین می کند که فرآیند به طور مؤثر ومطابق با استانداردهای فنی انجام شود .
ب - تجزیه و تحلیل قطعه فیزیکی
در این مرحله، تجزیه و تحلیل قطعه بهصورت دقیق و جزئی انجام میشود تا اطلاعات لازم برای تهیه دفترچه فنی به دست آید:
دیجیت و اندازهگیری: استفاده از ابزارهای مختلف مانند اسکنرهای 3D برای ایجاد مدل سهبعدی قطعه.که در این فرآیند اطلاعات دقیقی از هندسه قطعه بهدست می آید.
آنالیز مواد: شناسایی جنس مواد بهکار رفته در قطعه (مثلاً فولاد، آلومینیوم، پلیمر، یا آلیاژ خاص). این کار از طریق تستهای شیمیایی یا ابزارهای آزمایشگاهی با استفاده ازتوانمندیهای آزمایشگاههای معتبرانجام میشود.
بررسی ساختار قطعه: در صورتی که نیاز به تحلیل طراحی قطعه وجود داشته باشد، ساختار داخلی و خارجی قطعه مورد بررسی دقیق قرار می گیرد. این بررسی همچنین شامل تحلیل روش های مختلف تولید به کاررفته برای ساخت قطعه مانند موارد زیر می شود تا فرآیند تولید و ویژگی های ساختاری آن به طور کامل شفاف سازی گردد.
- ریختهگری (Casting)
- ماشینکاری (Machining)
- تراشکاری (Turning)
- فرزکاری (Milling)
- سوراخکاری (Drilling)
- سنگزنی (Grinding)
- جوشکاری (Welding)
- آهنگری (Forging)
- پرسکاری (Stamping)
- اکستروژن (Extrusion)
- قالبگیری تزریقی (Injection Molding)
- برش لیزری (Laser Cutting)
- برش پلاسما (Plasma Cutting)
- برش واترجت (Waterjet Cutting)
- پرینت سهبعدی (3D Printing/Additive Manufacturing)
- نورد (Rolling)
- خمکاری (Bending)
- سینترینگ (Sintering)
- لحیم سنگین (Brazing)
- تفجوشی ( Soldering)
ج - مدلسازی طراحی به کمک کامپیوتر
پس از انجام تجزیه و تحلیل دقیق قطعه و جمع آوری اطالعات الزم، این داده ها باید به مدل سه بعدی منتقل شده و فرآیند سطح سازی آغاز شود. طراحی این مدل با استفاده از نرم افزارهای پیشرفته ای همچون Inventor ،AutoCAD ،Catia و SolidWorks انجام میگیرد. این مدل، نمای دقیقی از هندسه قطعه است که تمامی ابعاد، اشکال و ویژگی های خاص آن را به طور کامل و دقیق نمایان می سازد.
ساخت مدل سهبعدی: طراحی مدل سهبعدی با استفاده از دادههای اندازهگیری شده در مراحل قبلی. این مدل باید تمامی جزئیات هندسی و ابعادی را شامل شود.
تحلیل مدل: پس از ایجاد مدل سه بعدی، تحلیل های مختلفی از جمله تحلیل تنش، دما و جریان سیالات، درصورت لزوم، بر روی مدل انجام می شود. این تحلیل ها به منظور اطمینان از کارایی و عملکرد قطعه در شرایط عملیاتی مختلف صورت می گیرد. بررسی دقیق این ویژگیها کمک می کند تا طراحی بهینه و عملکرد مطلوب قطعه در دنیای واقعی تضمین شود.
د - تهیه نقشههای فنی و دفترچه فنی
پس از ایجاد مدل سهبعدی، گام بعدی تهیه نقشههای فنی دقیق برای تولید قطعه است. این نقشهها باید شامل تمامی جزئیات لازم برای ساخت و مونتاژ قطعه باشند.
نقشههای ابعادی: در این مرحله، نقشههایی با تمامی ابعاد و تلورانس های ابعادی و هندسی قطعه ایجاد می گردد.
نقشههای مونتاژ: اگر قطعه بخشی از یک سیستم یا مجموعه بزرگ تر باشد، نقشه های مونتاژ نیز به طور ویژه تهیه می شود. این نقشه ها به طور واضح نحوه اتصال قطعه به سایر اجزاء سیستم را نشان می دهند و کارکرد آن درسیستم کلی را به طور کامل توضیح می دهد.
ویژگیهای سطحی: جزئیات مربوط به پرداخت سطحی، ضخامت لایه های پوششهای مختلف (در صورت وجود) و دیگرالزامات مهم همچون خصوصیات صافی سطح باید به طور دقیق در نقشه ها درج شوند. این ویژگی ها به تولیدکنندگان کمک می کنند تا قطعه را مطابق با استانداردهای موردنظر و با کیفیت بالا تولید کنند .
الزامات مواد و ساخت: در دفترچه فنی نوع مواد، استانداردهای مورد استفاده برای ساخت قطعه، روشهای تولید، و هر نوع فرآیند یا دستورالعمل خاص درج می گردد.
ه - شبیهسازی و بررسی عملکرد
در این مرحله، قطعه طراحیشده باید مورد ارزیابی قرار گیرد تا اطمینان حاصل شود که عملکرد آن مطابق با انتظار است. این کار میتواند از طریق شبیهسازیهای مختلف انجام شود:
تحلیل المان محدود : شبیه سازی با استفاده از روش تحلیل المان محدود به منظور بررسی استحکام، دوام و پاسخ قطعه در شرایط مختلف بارگذاری انجام می شود. این فرآیند به ویژه در شبیه سازی رفتار قطعه در برابرتنشها و نیروهای مختلف کاربرد دارد و می تواند نقاط ضعف احتمالی قطعه را پیش از ساخت فیزیکی شناسایی کند .
شبیه سازی عملکرد قطعه در محیط واقعی: برای قطعاتی که در سیستم های پیچیده تر مانند موتور یا ماشین آلات صنعتی به کار میروند، شبیه سازی عملکرد قطعه در محیط واقعی از اهمیت ویژه ای برخوردار است این شبیه سازیها به منظور شناسایی مشکلات احتمالی پیش از ساخت قطعه انجام می شود و کمک می کند تا درمراحل طراحی، مشکلاتی که ممکن است در عملکرد قطعه در دنیای واقعی پیش بیاید، شناسایی و رفع شوند .
و - تهیه مستندات تکمیلی
پس از اتمام طراحی و شبیهسازیها، باید مستندات تکمیلی مربوط به قطعه نیز تهیه شود. این مستندات شامل:
دستورالعملهای مونتاژ و نگهداری: این دستورالعمل ها برای اطمینان از استفاده صحیح و افزایش طول عمرقطعه در سیستم های واقعی تهیه می شوند. دستورالعمل ها شامل راهنمایی های دقیق در خصوص نحوه مونتاژ، نگهداری و مراقبت از قطعه برای حفظ عملکرد بهینه آن در طول زمان خواهند بود
تستهای کنترل کیفیت: برای تضمین کیفیت قطعه نهایی، دستورالعمل هایی برای آزمون ها و بررسی های کنترل کیفیت شامل آزمون های فنی و معیارهای ارزیابی عملکرد قطعه ارائه می شود. این تست ها به منظور اطمینان از انطباق قطعه با استانداردهای فنی و نیازهای کاربردی در نظر گرفته می شوند .
گواهینامههای استاندارد: در صورتی که قطعه نیاز به گواهینامه های استاندارد خاصی مانند ISO ،ASME ، ASTM یا دیگر گواهینامه های مربوطه داشته باشد، این گواهینامه ها در دفترچه فنی درج خواهند شد تا تطابق قطعه با استانداردهای بین المللی و صنعتی تضمین گردد.
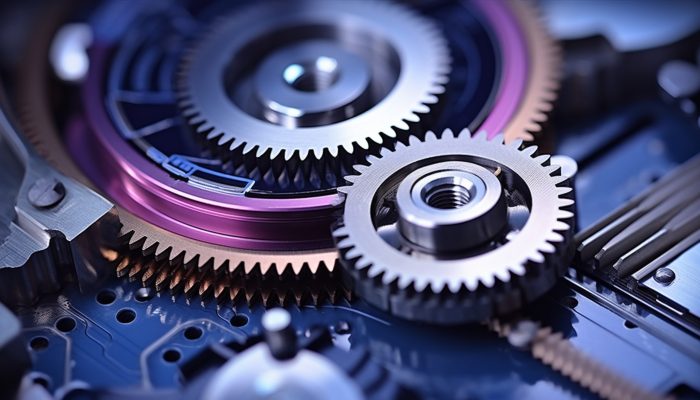
پس از تکمیل طراحی و تهیه نقشه های ساخت و دفترچه فنی، و پس از انجام تحلیل ها و بازسازی مدل ها، فرآیند تولید قطعات یدکی و تجهیزات با دقت بسیار بالا و مطابق با استانداردهای مورد نظر در کارگاه های ساخت، تحت نظارت و راهبری کارشناسان متخصص شرکت یکتا انتخاب سرافراز، به طور کامل پیگیری می شود تا تولید قطعه به درستی و بدون هیچ گونه خطای فنی انجام شود. این فرآیند شامل مراحل زیر است:
1- بررسی نقشه و برنامهریزی برای مراحل مختلف تولید، شامل زمانبندی و تخصیص منابع.
2- در این مرحله تهیه مواد اولیه مطابق با مشخصات فنی درج شده در نقشه ها و دفترچه فنی تهیه می شود.
کیفیت و استانداردهای مواد اولیه به طور کامل مورد بررسی قرار می گیرد تا با الزامات پروژه مطابقت داشته باشد.
3- انتخاب کارگاه های ساخت متناسب با نیازهای پروژه:
کارگاه های ساخت بر اساس نیازهای خاص هر مرحله ازفرآیند تولید، با توجه به ماشین آلات و فرآیندهای مورد نیاز، طبق توالی مشخص شده توسط کارشناسان شرکت انتخاب می شوند. این انتخاب به منظور حصول اطمینان از انجام صحیح و مؤثر تمامی مراحل تولید انجام می شود.
4- اطمینان از آمادگی ابزار و تجهیزات مورد نیاز:
در این مرحله، تمامی ابزارهای استاندارد و تجهیزات ضروری شامل قالبها، فیکسچرها، و ابزارهای برش بررسی و آماده میشوند تا فرآیند ساخت بدون وقفه و با دقت بالا انجام گیرد.
5- نظارت بر فرآیند ساخت:
کارشناسان شرکت در تمامی مراحل فرآیند ساخت حضور دارند تا اطمینان حاصل کنند که تمامی مراحل تولید طبق نقشه ها و برنامه ریزی های انجام شده و با رعایت دقیق استانداردها و دستورالعمل ها انجام می شود.
6- بازرسی و تست های کیفیت:
در طول فرآیند تولید، بازرسیهای دقیق و تستهای کنترل کیفیت در مراحل مختلف انجام می شود تا اطمینان حاصل گردد که قطعات تولیدی با مشخصات مندرج در نقشه ها و استانداردهای فنی مطابقت دارند و در صورت نیاز و درخواست کارفرما، هماهنگی برای حضور بازرس درهرمرحله نیز انجام خواهد شد.
7- مونتاژ قطعات در صورت نیاز:
اگر قطعات نیاز به مونتاژ داشته باشند، این مرحله با رعایت استانداردهای فنی ودستورالعمل های اجرایی انجام خواهد شد.
8- بررسی نهایی قطعه:
قبل از تحویل یا بسته بندی، قطعات نهایی از نظر ابعاد، کیفیت ساخت و تطابق با نقشه ها به طور کامل بررسی می شوند. در صورت نیاز و درخواست کارفرما، هماهنگی برای حضور بازرس در این مرحله نیز انجام خواهد شد.
9- بسته بندی ایمن قطعات:
قطعات با دقت و به گونه ای بسته بندی می شوند که از آسیب دیدگی در طول حمل ونقل جلوگیری شود. پس از بسته بندی، قطعات برای تحویل به مشتری یا ارجاع به دیگر مراحل ساخت درکارگاه های دیگر آماده خواهند شد.
10- مستندسازی دقیق فرآیندها:
تمامی مراحل تولید، نتایج کنترل کیفیت، گواهینامه ها و مستندات مرتبط به دقت ثبت و مستند می شوند تا در صورت نیاز به ارجاع در آینده، تمامی اطلاعات به راحتی در دسترس باشد و به طور شفاف به کارفرما ارائه گردد.